There are many ways to use heat in manufacturing processes,
like drying, curing, sanitation, and more. By following these steps and making
your heat use more efficient, you can save money and reduce emissions.
Check
Your System
Older heat
systems might not be very efficient. You can save money and reduce emissions by
understanding how efficient your system is. Look at your fuel use compared to
your system's rating and consider installing heat meters to track efficiency.
When it's sensible, think about replacing old equipment with newer, more
efficient models. It’s important to note that replacing equipment may be a
longer-term, more expensive measure to implement.
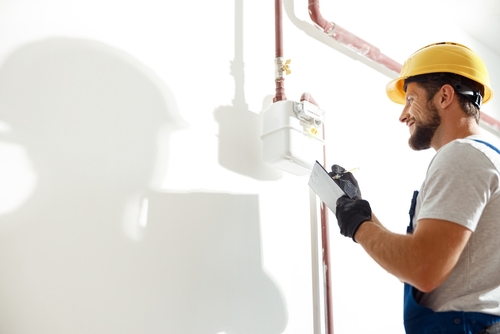
Optimize
scheduling
Take a look
at your work schedules; can you operate your equipment for shorter,
high-capacity periods? Small changes can yield significant efficiency gains. Aim
for full loads when using dryers, ovens, and tanks as it's more energy
efficient than doing multiple smaller loads.
Explore
alternative methods: Sometimes, you can reduce the need for heat altogether.
For example, consider mechanical de-watering techniques like pressing or
centrifuging to minimize your reliance on heating.
Using
waste heat
Don't let
excess heat escape unused. Capture and repurpose it for various applications,
from preheating materials to warming workshop spaces. This not only conserves
energy but also trims costs.
Train
Your Staff
Teach your
staff about the right temperatures for processes. Sometimes, you can lower the
heat and still get the same quality results. Also, make sure your staff knows
how long it takes for equipment to heat up. This helps prevent unnecessary
energy use.
Dryers
Dyers play
an important role in industries like chemicals and pharmaceuticals. Therefore,
they likely account for a significant amount of your energy consumption. Here
are some ways you can make them more efficient.
Manage
moisture levels
Controlling
moisture in your materials can reduce the need for extensive drying. Prevent
excessive water from entering the feedstock during storage or consider product
modifications to lower moisture content.
Regular
Maintenance
Keep dryers
in prime condition. Detect and address issues like damaged insulation, clogged
air filters, air leaks, and product quality promptly to maintain efficiency.
Optimize
Scheduling
Effective
scheduling ensures equipment is preheated only when necessary. Identify areas
where dryers run unnecessarily and consider automatic controls to manage
heat-up times more effectively.
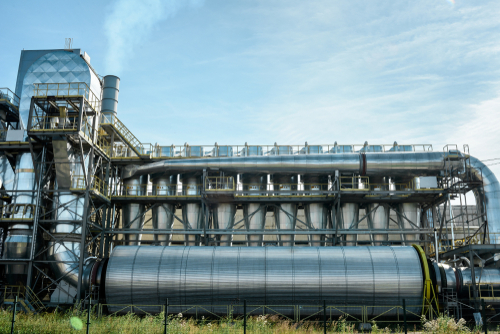
Ovens
Ovens are
often used in manufacturing for tasks such as baking and curing. These are some
of the ways you can save energy used to run your ovens.
Inspect
and Maintain Ovens
Regularly
inspect your ovens for worn seals, damaged insulation, or inefficient
operations. Prompt repairs prevent wasted heat energy.
Streamline
Process Control
Determine
the minimum heating time required and install automatic process controls to minimize
heat-up periods, ensuring ovens are only heated as needed.
Preserve
Heat
If you have
batch ovens, ensure doors aren't left open longer than necessary. For
continuous ovens, consider using air curtains to keep hot air inside, allowing
staff to work close to open ends comfortably.
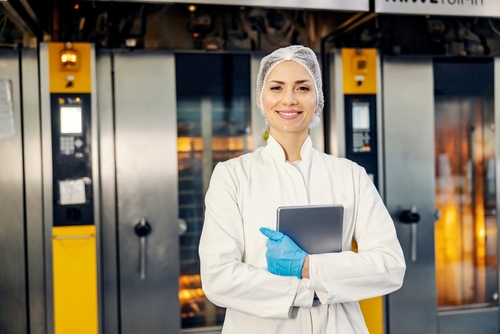
Tanks holding heated liquids
Tanks are
often used in wet processes such as washing, glazing, heating caustic oil, and
more.
Reducing
Evaporation Losses
Heat often
escapes from tank solutions due to surface evaporation. Reduce these losses by
fitting tank lids and regulating solution agitation and extraction. This can
slash heat loss by more than 50%.
Insulate
Tanks
Cover tanks
at night to curb heat loss and conserve energy. Proper insulation, with at
least 50mm on sides and lids, can result in potential savings of up to 90% of
heat energy.
Temperature
and Heating Control
Avoid
over-preheating and heating during idle tank periods. Regularly maintain and
calibrate temperature sensors and controls to save energy and maintain product
quality.
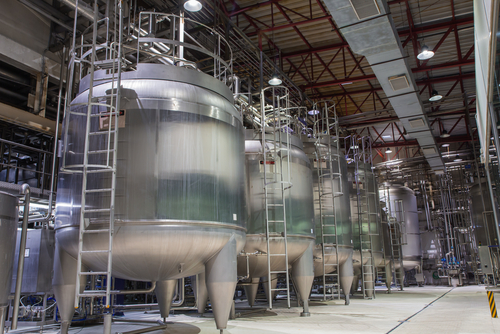